Die International Automotive Components (IAC) präsentiert auf der Fachausstellung zum diesjährigen internationalen VDI-Kongress „Kunststoffe im Automobilbau” auf vertikaler Integration basierende neue Lösungen für mehr Nachhaltigkeit im Fahrzeuginnenraum. Im Fokus stehen […]
Die International Automotive Components (IAC) präsentiert auf der Fachausstellung zum diesjährigen internationalen VDI-Kongress „Kunststoffe im Automobilbau” auf vertikaler Integration basierende neue Lösungen für mehr Nachhaltigkeit im Fahrzeuginnenraum. Im Fokus stehen eine umweltfreundliche Handschuhfachabdeckung, die neue Hybridfleece Molding Spritzgießtechnik, ein Bioharz-Sandwich-Werkstoff für Kofferraumladeflächen sowie zweifarbige Häute für Instrumententafeln, hergestellt im Fastkast Slush-Verfahren.
„Dank globaler Entwicklungs- und Fertigungskapazitäten ist IAC in der Lage, Inhouse-Lösungen für die gesamte Wertschöpfungskette von Fahrzeuginnenräumen anzubieten. Mittels vertikaler Integration können wir unsere Kunden mit vielen verschiedenen Services unterstützen, dazu zählen Material- und Produktdesign, Entwicklung, Werkzeugtechnik, Fertigung und Logistik. So entstehen individuelle Lösungen, die wir effizient und in konstanter Qualität produzieren können“, erklärt Rien Segers, Senior Vice President Engineering & Development für Europa bei IAC.
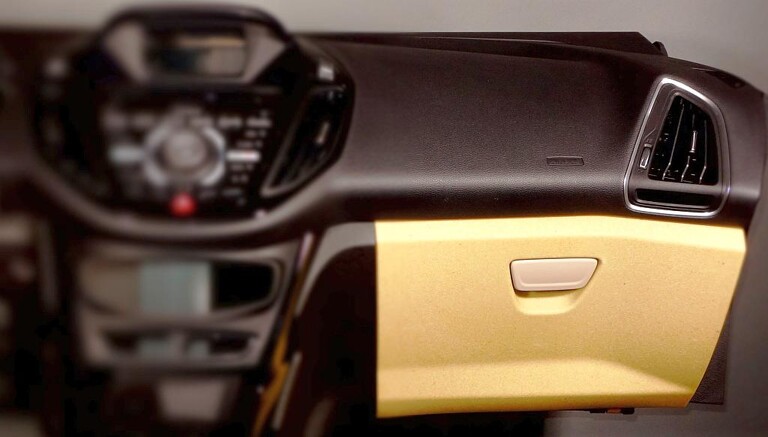
Die vollständig spezifizierte Handschuhfachabdeckung aus Naturfaser ist auf der Produktionslinie des Ford B-Max im IAC-Werk in Bals, Rumänien, entstanden. (Foto: IAC)
Die umweltfreundliche Handschuhfachabdeckung ist die erste Interieur-Anwendung, die IAC aus einem neu entwickelten Polypropylen-Sisal-Verbundwerkstoff unter Serienproduktionsbedingungen fertigt. Das Material entstand im Rahmen eines dreijährigen Modellierungs- und Simulationsprojektes unter der Leitung des Ford Forschungszentrums in Aachen, gefördert vom Bundesministerium für Ernährung und Landwirtschaft (BMEL). Die Abdeckung wurde auf der aktuellen Ford B-MAX Linie im rumänischen IAC Werk Bals gefertigt. Im nächsten Schritt entwickelt IAC Möglichkeiten, weitere mehrfarbige Innenraumkomponenten aus Naturfaser-Verbundwerkstoffen herzustellen.
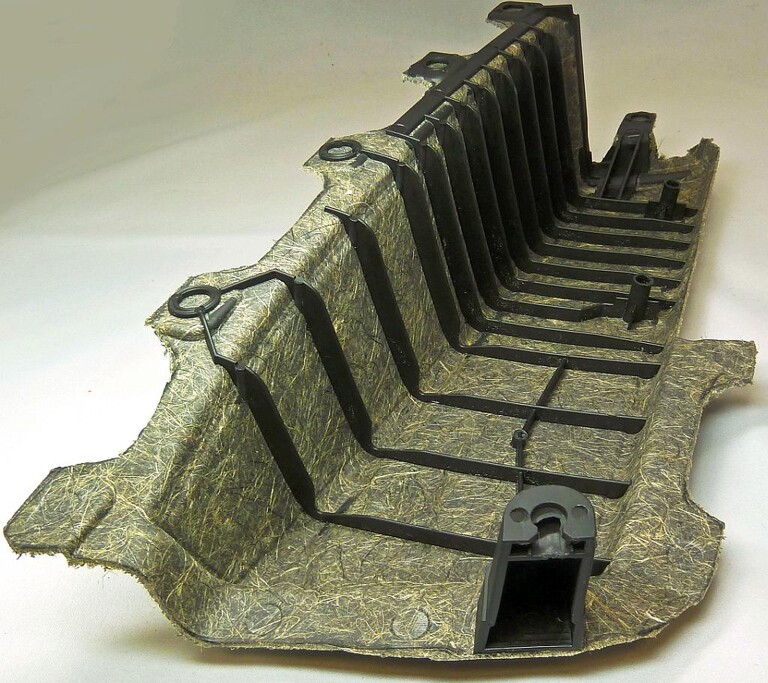
Leicht, robust und einfach herzustellen: Mit IAC Hybridfleece gegossene Armlehne mit recycelter Kohlenfaser. (Foto: IAC)
Branchenweit herrscht eine starke Nachfrage nach qualitativ hochwertigen, nachhaltigen Materialien, die sich in bereits bestehende Prozesse integrieren lassen. Die neue Hybridfleece Molding Technologie von IAC ermöglicht die Herstellung von Fleece aus Naturfaser, Glas oder recycelter Kohlenfaser. Das Fleece lässt sich im konventionellen Spritzgussverfahren zu Trägerelementen von Innenraumkomponenten formen. Im Vergleich zu gewöhnlichen Komponenten erlauben Hybridfleece Molding Produkte Gewichtseinsparungen von bis zu 50 Prozent bei gleichbleibender Steifigkeit und Funktionalität. Mit speziellen Fleece-Rezepturen, der eigenen Matrix-Produktion und exklusiven Bezugsquellen stellt IAC eine durchgehend hohe Materialqualität sicher.
Die Hybridfleece Molding Technologie lässt außerdem eine besonders hohe Materialflexibilität in der Fleece-Rezeptur zu. Dies erlaubt die Nutzung für viele robuste Verkleidungskomponenten im Innenraum. Hinzu kommt die geringere Prozesskomplexität, da sich die Produktion der Hybridmatrix und das Einspritzen von Verstärkungen bzw. Halterungen ohne zusätzliches Schweißen und Kleben in derselben Spritzgießmaschine in einem Schritt durchführen lassen.
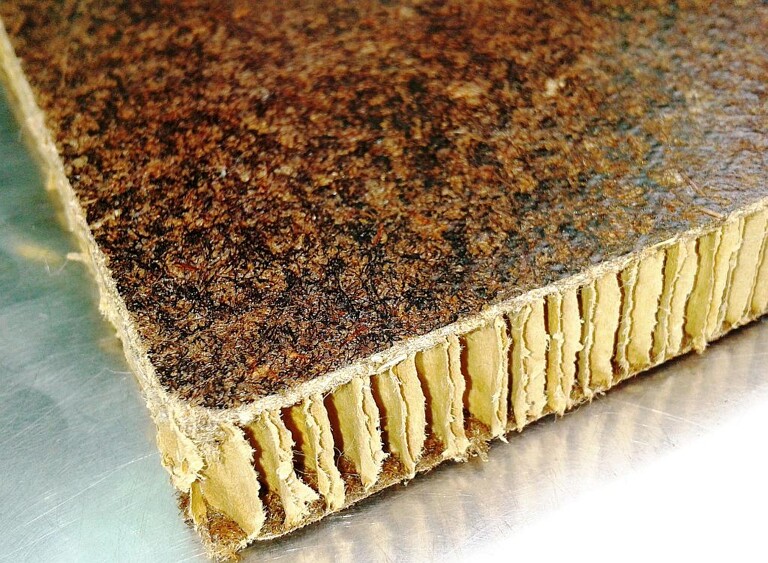
In dem Sandwich-Material für Kofferraumladeflächen kombiniert IAC Bioharz mit einem Wabenkern aus recyceltem Papier für nachhaltige Interieurs. (Foto: IAC)
Mit dem auf Bioharz basierenden Sandwich-Werkstoff für Kofferraumauskleidungen unterstützt IAC Automobilhersteller, die CO2-Bilanz ihrer Fahrzeuge durch den Einsatz erneuerbarer, nachhaltiger und recycelter Innenraummaterialien zu verbessern. Der Verbundwerkstoff besteht aus Naturfaserplatten mit einem Bioharz-Bindemittel und einem Wabenkern aus recyceltem Papier. Das Bioharz-Sandwich-Substrat ist zur Auskleidung der Kofferraumladefläche entwickelt. Der Werkstoff zeichnet sich im Vergleich zu herkömmlichen Polyurethan-Glasfaser- oder Papierwaben-Systemen durch verbesserte Materialeigenschaften und ein optimiertes Gewicht aus. Das glasfaserfreie Material kann in einem Standard-Duroplast-Pressverfahren mit besonders wenig Ausschuss hergestellt werden.
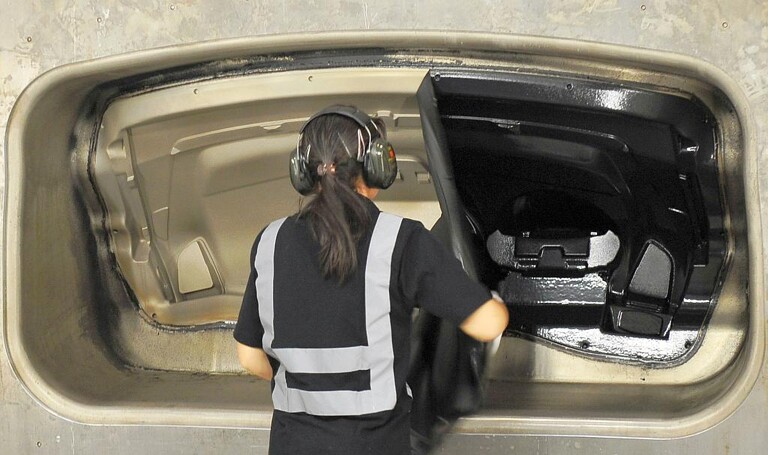
IAC fertigt mit Fastkast auf effiziente Weise qualitativ hochwertige, robuste, zweifarbige Häute. (Foto: IAC)
Mit der Erweiterung der eigenen Slush-Technologie Fastkast ist IAC jetzt in der Lage, in einem Prozess Häute in zwei Farbtönen herzustellen. Die Fastkast-Häute für Instrumententafeln verfügen über eine verbesserte Optik und Langlebigkeit bei gleichzeitig reduzierter Dicke. Der besonders niedrige Energie- und Materialverbrauch des Prozesses ist ein Vorteil in punkto Nachhaltigkeit. Eine zweifarbige Produktion ermöglicht Fahrzeugherstellern die effiziente Kombination aus nachhaltiger Fertigung und individuellen, hochwertigen Innenräumen.