Die Touchskin-Bedienoberflächen des österreichischen Technologie-Entwicklers Plastic Electronic GmbH, Linz, haben die dritte Dimension erobert. Sie eröffnen neue Möglichkeiten für ein organischeres Gerätedesign, das die Grenzen zwischen Form und Funktion zunehmend […]
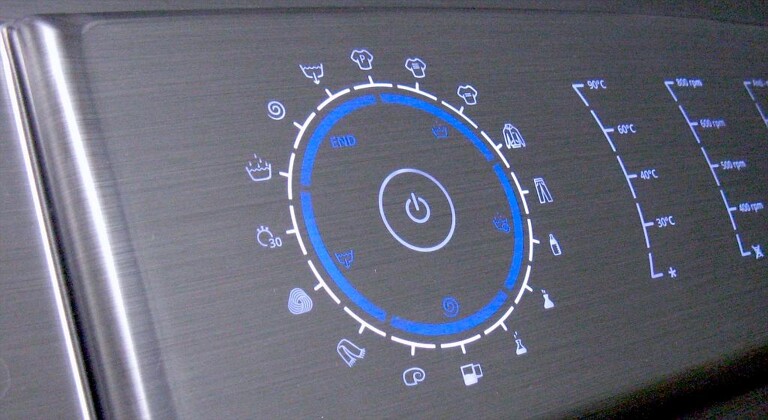
Die erweiterte 3-dimensionale Formbarkeit der Touchskin-Bedienpaneele erlaubt die organische Integration von Sensorflächen in Geräteoberflächen für den Haushalt und in Automobilen. (Foto: Plastic Electronic)
Die Touchskin-Bedienoberflächen des österreichischen Technologie-Entwicklers Plastic Electronic GmbH, Linz, haben die dritte Dimension erobert. Sie eröffnen neue Möglichkeiten für ein organischeres Gerätedesign, das die Grenzen zwischen Form und Funktion zunehmend aufhebt. Und dies zu vergleichsweise geringeren Gesamtkosten. Wie geht das? Hinter einer Touchskin-Geräteoberfläche, ob eben oder räumlich gekrümmt, steckt ein mehrlagig verklebter Folienverbund, dessen Einzellagen samt spezifischer Beschichtungen die Funktionsträger sind. Dazu zählen die Sensorflächen samt den elektrischen Leiterbahnen zu den Steuerungs-Leiterplatten, ein LED-Beleuchtungssystem, das grafische Bedienlayout und das Oberflächen-Dekor. Und, das alles innerhalb einer stabilen Verbundplatte mit einer Dicke von lediglich 2,5 bis 3 mm. Diese, von Plastic Electronic als Multi Skin bezeichneten Verbund-Bauteile lassen sich entweder kleinflächig in Spritzgussteile integrieren oder großflächig als umfassende Gehäusekomponenten einsetzen. Der nachstehende Bericht gibt einen Überblick über die aktuellen Möglichkeiten.
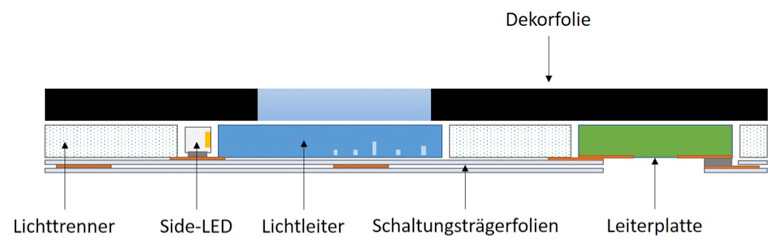
Multiskin-Folienverbund-Bauteile sind mehrlagige Folien-Compounds, die zu stabilen Bauteilen laminiert sind. Der 2,5 bis 3 mm dicke Folienverbund besteht (von oben nach unten) aus der Dekorfolie (Bedienoberfläche), der zentralen Folie mit dem LED-Beleuchtungssystem und den Leiterplatten, sowie der Schaltungsträgerfolie. (Abb.: Plastic Electronic)
„Folien mit funktionellen Strukturen zu versehen und daraus sensible Geräteoberflächen zu entwickeln, ist der rote Faden unserer 10-jährigen Firmengeschichte“, fasst Philipp Weissel, der geschäftsführende Gesellschafter des Linzer Technologie-Entwicklers zusammen. Aktuell steht man bei der zweiten Generation der bauteilintegrierten Sensoroberflächen unter dem Produktnamen Touchskin, deren Funktionen durch den eingangs erwähnten Multiskin-Folienverbund beigesteuert werden.
Die vielen Funktionen des Multiskin-Folien-Verbundes
Dessen wesentlicher Bestandteil ist die Schaltungsträger-Folie. Über sie laufen die Bediensignale zur elektronischen Gerätesteuerung sowie die Versorgung der elektronischen Bauteile. Sie muss dünn, flexibel, 3D-verformbar und für den Prozess der Bestückung mit elektronischen Bauteilen geeignet sein. Diese Kriterien erfüllen Polyester-Folien. Wenn keine Bauteilbestückung erfolgt, z.B. für Touch-Sensoren, können PET-Folien verwendet werden. PEN-Folien sind einzusetzen, wenn bei der Herstellung, vor allem beim Bestückungsprozess, höhere Temperaturbelastungen entstehen.
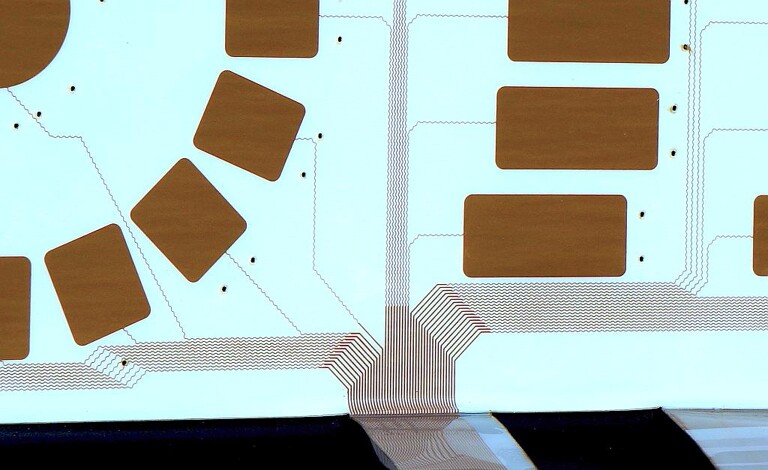
Ein Leiterbahn-Design mit einer Mäander- bzw. Wollfadenstruktur ermöglicht die Kompensation von Längenänderungen während des Tiefziehprozesses zur 3D-Verformung. (Foto: Reinhard Bauer)
Auch die Leiterbahnen müssen die geforderten Eigenschaften aufweisen und darüber hinaus die bei der Verformung auftretenden Verstreckungen mitmachen, ohne die Leitfähigkeit zu verlieren. Als Beschichtungsprozess für die Leiterbahnen kommt entweder ein Druckverfahren mit Silberpaste oder das Aufdampfen oder Kaschieren von Kupferschichten in Frage. Ersteres nur dann, wenn die Leitungsstruktur nicht zu groß und zu komplex ist. Um die Kupferleiterbahnen verstreck- bzw. verformbar zu machen, stehen spezielle Produktionsverfahren oder Designs zur Verfügung. So kann beispielsweise eine Leiterbahn in Mäanderform in weiten Grenzen gedehnt werden ohne zu reißen. Aufdampfverfahren ermöglichen die Aufbringung dünner Kupferschichten (kleiner 1 µm), die sich ebenfalls sehr stark verstrecken lassen (größer als 70 %) und kostengünstig in der Herstellung sind.
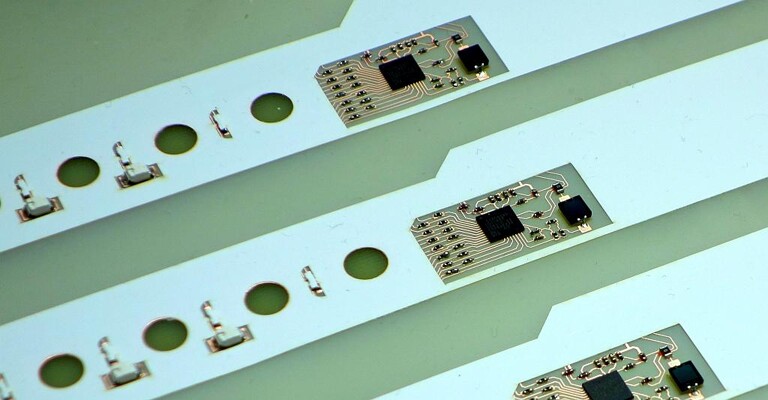
Für Leitstrukturen, über die größere Ströme transportiert werden, werden Kupferschichten aufkaschiert, die durch Ätzverfahren strukturiert werden. (Foto: Reinhard Bauer)
Aufgrund der geringen Schichtdicke und der damit geringen Stromtragfähigkeit sind letztere allerdings nur zur Signalübertragung wie der Touch-Sensor-Signale, geeignet. Für die Versorgung von LEDs werden Leiterbahnen aus 18 µm dickem Elektrolytkupfer verwendet. Das Elektrolytkupfer wird dabei auf die Folie laminiert und dann durch ein klassisches Ätzverfahren strukturiert.
Die Verbindung der elektronischen Bauteile mit den Leiterbahnen auf der Folie erfolgt entweder durch Niedertemperatur-Löten oder durch Kleben mit leitfähigen Klebepasten. Niedertemperaturlöten wird bevorzugt, je kleiner die Bauteile und deren Kontaktabstand sind.
Was kann die Touchskin-Bedienoberfläche?
Touchskin-Bedienflächen sind nahtlose Oberflächen mit durchgängiger Optik. Dafür eignen sich Materialien wie Kunststoffe, Holz oder Glas. Zu beachten ist, dass diese Oberfläche keine oder nur eine sehr geringe Leitfähigkeit aufweisen darf. Leitfähige Oberflächen (z.B. aus Metall) würden wie eine Schirmlage wirken und die Touch-Bedienung unmöglich machen.
Die Oberflächengestaltung der Oberflächenfolie erfolgt durch Druckverfahren, und zwar so, dass sie an jenen Stellen, wo sich Leuchtelemente befinden, lichtdurchlässig (transluzent) ist und zusätzlich Farbe, Dichte und Homogenität der Lichtemission bestimmt werden. Auch können die lichtdurchlässigen Bereiche so gestaltet sein, dass sie nur bei aktivierter Beleuchtung erkennbar sind (Verschwinde-Effekt). Bei Bedienoberflächen, die keine Leuchtelemente benötigen, können die Oberflächen auch vollständig aus nichttransparenten Materialien bestehen.
Verwendet werden meist transparente Folienmaterialien wie PMMA, PC oder PET, die im Siebdruck oder mit anderen Druckverfahren entweder an der Hinter- oder an der Vorderseite bedruckt werden.
Die Oberfläche wird je nach Anforderung zusätzlich mit einem transparenten Schutzlack (z.B. Hard-Coat) oder einem transparenten Kunststoff (z.B. transparenter Thermoplast oder PU) überzogen. Das erhöht die Widerstandsfähigkeit der Oberfläche gegenüber Fremdeinflüssen (mechanische oder chemische Beständigkeit, Anti-Fingerprint). Dabei können sowohl matte, als auch glänzende bis hochglänzende Oberflächen realisiert werden.
Vom lokalen Bedienfeld zur großflächigen Gerätehaut ist alles möglich
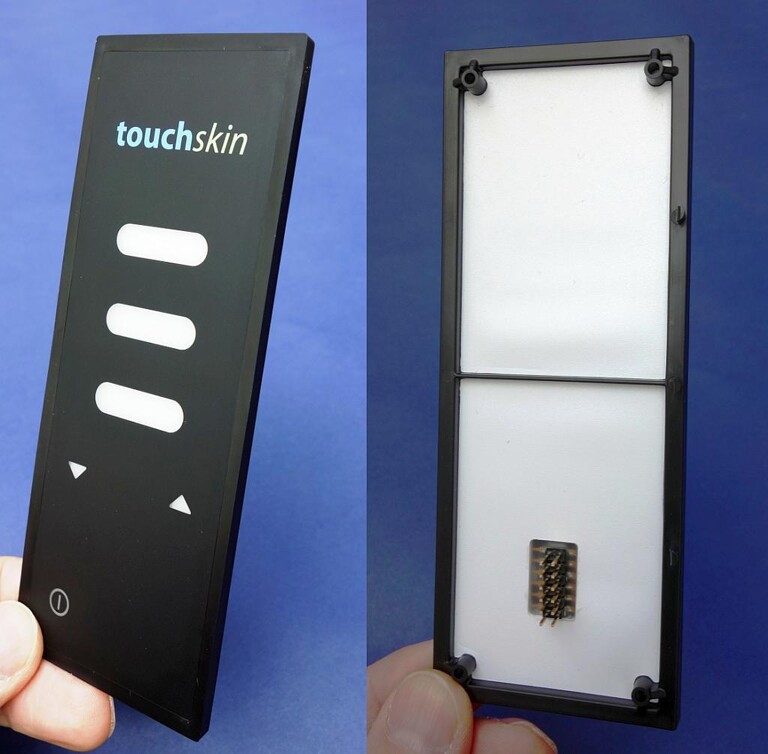
Eine Möglichkeit zur Reduktion der Schwindungseffekte auf den Folienverbund ist das Umspritzen mit einer Rahmenstruktur, die gleichzeitig Träger der mechanischen Schnittstellen zu den Partnerteilen ist, hier am Beispiel einer 2,2 mm dicken Multiskin-Verbundplatte mit integriertem Beleuchtungssystem und 12-Pin-Steckverbindung. (Fotos: Schöfer)
Das Potenzial der Touchskin-Technik ist, Schalter oder Schieberegler-Funktionen in fugenloser Touch-Ausführung direkt in einen Kunststoff-Bauteil zu integrieren oder mit anderen Oberflächen, wie Glas oder Holz, durch Hinterkleben zu kombinieren. Der Vorteil ist die Funktionsintegration auf engstem Bauraum und die deutliche Reduzierung der Systemkomponenten und damit des Montageaufwands. Kleine bis mittelgroße Multiskin-Verbundteile können als lokale Bedieninsel durch Umspritzen direkt in Kunststoffgehäuse eingefasst werden. Anwendungsbeispiele sind Tastenfelder von Geräte-Fernbedienungen oder Bedienflächen auf Tür-Zierleisten oder Lenkrädern im Auto. Das Größenlimit für diese Anwendungen wird durch die Verarbeitungsschwindung des Spritzgussteils und dessen Krafteinwirkung auf den Verbundteil bestimmt bzw. die technische Möglichkeit zur Entkoppelung dieses Einflusses.
Große Multiskin-Bauteile, beispielweise Bedienkonsolen für Waschmaschinen oder Geschirrspüler, können nicht mehr umspritzt werden, ohne dass sie durch den Verzugseffekt deformiert werden. Daher empfiehlt sich mit zunehmender Größe, den Folienverbund und die Spritzgießstruktur separat zu fertigen und durch einen Montagevorgang, z. B. durch Kleben mit einer Stütz- bzw. Haltestruktur am Gerät zu fixieren.
Bedien-Terminals neu gedacht
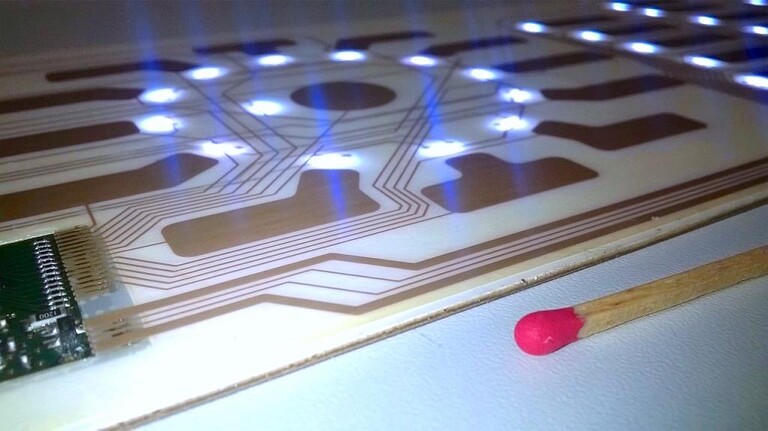
Detailansicht des Folienverbundes: In der zentralen Lichtfolie befinden sich eingesetzte Lichtleitbereichen, die von jeweils einer Leuchtdiode mit seitlichem Lichtaustritt angestrahlt werden. Die Lichtfolie ist mit einer Folie abgedeckt, auf der sich die Leitstrukturen zur Ansteuerung der Sensorfunktionen befinden. (Foto: Plastic Electronic)
Welches Potenzial in der Touchskin-Technik steckt, wurde von Plastic Electronic durch ein Waschmaschinendisplay mit 40 hinterleuchtbaren Bedientasten und einer neuen, selbst erklärenden Bedienlogik vorgestellt. Dazu Philipp Weissel: „Der größte Evolutionsschritt bei unseren Bedienoberflächen ist die gelungene Integration eines verformbaren LED-Beleuchtungssystems.“ Denn, durch die notwendige Wanddicke der zentralen Licht-Folie von rund 1,5 mm mutierte der Folienverbund zu einer stabilen Sandwichplatte. Durch gezielte Abstimmung aller Folien- und Beschichtungs-Eigenschaften innerhalb des Verbundes konnte eine weitgehende Verformbarkeit der Sandwichplatte erreicht werden. Damit kann die Bedienfläche nun zum großflächigen Bedienterminal als Teil der Gerätehaut mutieren.
Großflächige Multiskin-Bauteile für innovative Gerätedesigns
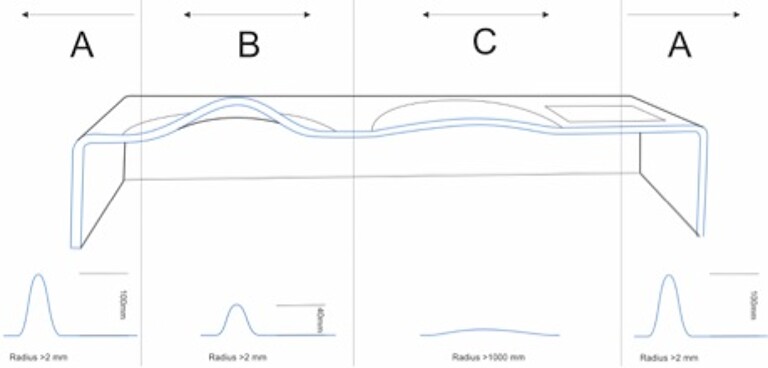
Designrichtlinie für die Touchskin-Bedienoberflächen auf Basis der aktuell möglichen Verstreckungsverhältnisse. Grundsätzlich ergeben sich aktuell folgende Verformungslimits:
A: Folien-Bereiche ohne Leucht- und Bedienelemente können in der Höhe bis zu 100 mm mit einem minimalen Krümmungsradius von 2 mm verstreckt werden. B: Rund um Bedienelemente (ohne Leuchtelemente) ist eine Höhen-Verstreckung bis zu 40 mm mit einem minimalen Krümmungsradius von 2 mm möglich. C: Rund um Leuchtelemente sind Wölbungen mit einem Radius von 1000 mm und größer möglich. (Abb.: Plastic Electronic)
Dazu Weissel: „Das wichtigste Potenzial unseres jüngsten Entwicklungserfolges sind die viel weiter gesteckten Grenzen für das Geräte-Design. Dieses setzt zunehmend auf organische Formen mit abgerundeten, gewölbten Flächen. Dabei wirken übliche flache Touch-Screens oder ebene Tasten-Terminals zunehmend als Fremdkörper. Unsere Alternative dazu sind dreidimensional geformte Gehäuse-Oberflächen mit der, von uns entwickelten Funktionsintegration.“
Auf die Bedienung von „Weißeware-Geräten“ bezogen, bedeutet dies, dass nicht nur die präzise Anpassung einer Bedienoberfläche in das Gerätedesign möglich ist, sondern darüber hinaus zusätzliches Potenzial zur Integration von geometrischen Strukturen zur Fingerführung (Rillen, Wellen, Ringnuten) vorhanden ist. Ein weiterer Vorteil der Folien-Verbunde ist die Flexibilität bei der Verbundteil-Herstellung. Sprach-, Farb- und Dekorvarianten lassen sich durch Austauschen der Dekorfolie auch bei kleinen Losgrößen einfach und schnell realisieren.
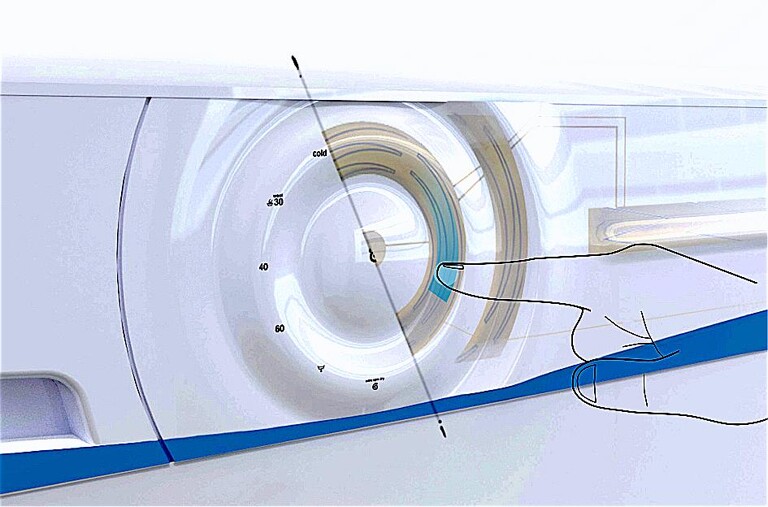
Mit der aktuellen Evolutionsstufe der Multiskin-Folienverbunde lassen sind dreidimensional geformte Bedienoberflächen, beispielsweise mit Profilbereichen zur Fingerführung herstellen. (Konzeptstudie: Plastic Electronic)
Weissel fasst zusammen: „Touchskin dreidimensional bietet großes Potenzial zur Kostenreduktion bei Bedienterminals und ebenso großes Potenzial für die Weiterentwicklung des Gerätedesigns. Durch unsere Position als unabhängiges Technologie-Unternehmen sind wir in die Lage, allen Geräteproduzenten zur Verkürzung der Entwicklungsphasen sowohl mit einem Design-Guide, als auch für die Prototypen-Entwicklung zur Verfügung stehen zu können.“