Der Strang-Granulieranlagen-Spezialist RE-Scheer, Korntal-Münchingen , hat seine Maschinenpalette um eine neue Baureihe für kleinere bis mittlere Durchsatzmengen erweitert. Die Geräte unter der Typenkennung SGS L-10 sind in vier Baugrößen mit […]
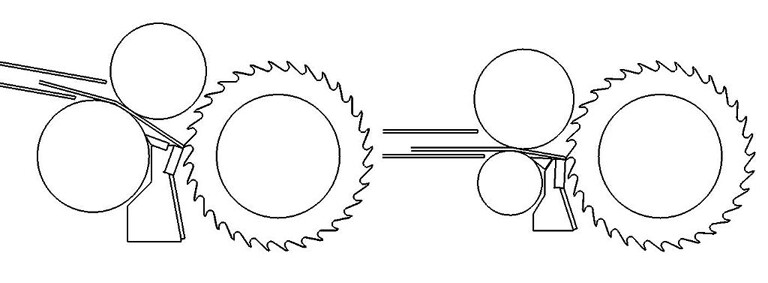
Bei der neu konzipierte Schneidgeometrie legen die Kunststoffstränge eine kürzere ungeführte Strecke zwischen Abzugswalzen und Schnittstelle zurück, kommen damit gerader an können und in einem nahezu rechten Winkel zur Längsachse geschnitten werden. (Abb.: Reduction Engineering)
Der Strang-Granulieranlagen-Spezialist RE-Scheer, Korntal-Münchingen , hat seine Maschinenpalette um eine neue Baureihe für kleinere bis mittlere Durchsatzmengen erweitert. Die Geräte unter der Typenkennung SGS L-10 sind in vier Baugrößen mit Arbeitsbreiten von 100 bis 400 mm und Durchsätzen bis zu 4 t/h verfügbar und werden parallel zu den SGS L-Geräten angeboten. Die wesentlichsten Vorteile der neuen Geräte sind die kompaktere Bauweise, eine besonders bedienfreundliche Konzeption durch die Produktwechsel bzw. der Tausch von Verschleißteilen mit weniger Personal und in kürzerer Zeit durchgeführt werden können, und nicht zuletzt eine neue Schneidgeometrie, die die Granulatqualität vor allem bei der Verarbeitung von elastischen und spröden Materialien erhöht.
Vereinfachte Handhabung verkürzt Wartungszeiten
Bei der Entwicklung der neuen Baureihe mit zweiseitiger Lagerung hatten die spezifischen Anforderungen kleiner bis mittlerer Produktionslose mit einer hohen Typenvielfalt Vorrang. Die Mechanik der Strangführung wurde von Grund auf neu konzipiert. Das Resultat ist einerseits eine neue Schneidgeometrie mit einer optimierten Anordnung von Schneidrotor, Einzugswalzen und Ambossmesser relativ zueinander, andererseits ein neues Bedienkonzept für die Reinigungs- und Umrüstvorgänge.
Die neue Schneidgeometrie minimiert die ungeführte Länge der Kunststoffstränge zwischen den Einzugswalzen und der Schneidkante. Dadurch laufen die Stränge ruhiger und gleichmäßiger zum Schneidrotor. Dieser Effekt ist grundsätzlich für alle Kunststofftypen gegeben, jedoch bei der Verarbeitung von elastischen Kunststoffen in besonders hohem Maß von Vorteil. Die neue Anordnung des Ambossmessers ergibt einen nahezu rechtwinkeligen Schnitt zur Strang-Längsachse und reduziert somit wesentlich den Staubanteil beim Schnitt spröder Kunststoffe.
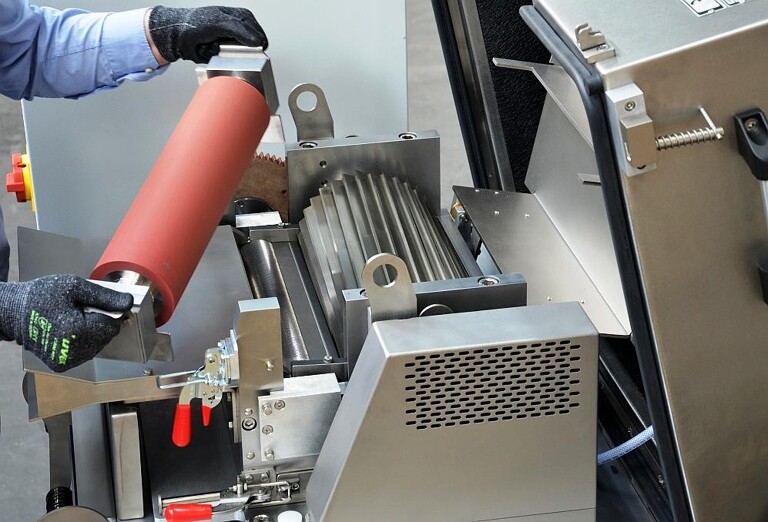
Die Frontseite des Schneidgehäuses mit Einlaufschacht und Einzugswalzen ist über Schnellverschlüsse schnell und werkzeuglos zugänglich. Damit verkürzen sich die Stillstandszeiten beim Produktwechsel bzw. dem Tausch von Verschleißteilen um 30 bis 40 %. (Foto: Reduction Engineering)
Bei der Konzeption der neuen Schneidgeometrie wurden alle Systemkomponenten inklusive der Schneidkammer in Richtung hoher Reinigungs- und Servicefreundlichkeit überarbeitet. Das wichtigste Ergebnis sind durchwegs leichtere Walzeneinheiten. Die obere Einzugswalze ist um 15 %, die untere um 60 % leichter. Dadurch kann das Ausheben beim Reinigungsvorgang ohne Hebezeug und von nur einer Person durchgeführt werden. Beim Ausbau der unteren Einzugswalze, sowie der Rotorlagerung sind nun wesentlich weniger Schraubverbindungen zu lösen, die obere Einzugswalze kann gänzlich ohne Werkzeug ausgebaut werden. Der Schneidspalt zwischen Ambossmesser und Schneidrotor wird über leicht zugängliche Zug- und Druckschrauben eingestellt. Die Frontseite des Schneidgehäuses mit Einlaufschacht und Einzugswalzen ist auf einer Präzisions-Linearführung verschiebbar montiert, und ermöglicht somit einen leichten und werkzeuglosen Zugang zum Schneidgehäuse. So kann das Ambossmesser gewechselt werden, ohne dass vorher der Schneidrotor ausgebaut werden muss. Mit dem neuen Gerätekonzept verkürzen sich die Stillstandszeiten beim Produktwechsel bzw. dem Tausch von Verschleißteilen um 30 bis 40 %.
Reduzierte Schallemission
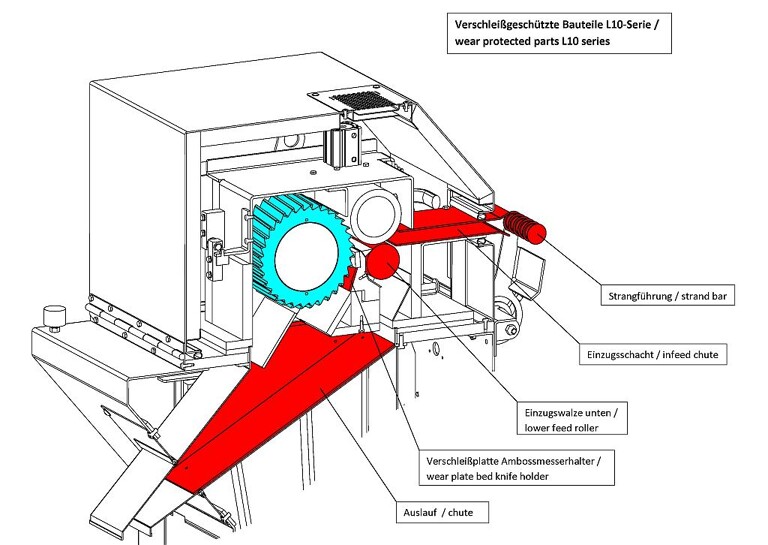
Zur Verarbeitung von Kunststoff-Compounds mit einem höheren Anteil an abrasiv wirkenden Füll- und Verstärkungsstoffen ist die neue Baureihe optional auch in verschleißfester Ausführung (rot gekennzeichnete Komponenten) lieferbar. (Foto: Reduction Engineering)
Die neuen Granulatoren haben eine wirksame Schalldämmung. Eine akustisch optimierte Schallhaube und eine vollständige Körperschallentkopplung zwischen Schneidgehäuse und Maschinengestell gewährleisten einen Schallpegel von unter 85 dB(A) nach DIN. Der Schallpegel konnte gegenüber der SGS-L Baureihe um bis zu 5 dB(A) reduziert werden. Bei der Neukonstruktion konnte auch die Baugröße insgesamt, insbesondere die benötigte Aufstellfläche verkleinert werden – ein Faktum, das vor allem bei begrenztem Produktionsflächenangebot von Bedeutung sein kann. Sicherheitsvorrichtungen sorgen dafür, dass die Schallhaube erst nach Stillstand des Schneidrotors geöffnet werden kann.
Verschleißteile kompatibel
Trotz der sehr weitgehenden Überarbeitung des Granuliersystems wurden die Verschleißteile, wie Ambossmesser und Schneidmesser-Segmente unverändert beibehalten, sodass kein Zusatzaufwand bei der Lagerhaltung einkalkuliert werden muss. Für die Verarbeitung von Kunststoff-Compounds mit einem hohen Anteil an abrasiv wirkenden Füll- bzw. Verstärkungsstoffen wird optional ein spezieller Verschleißschutz angeboten.
Die neuen Granulatoren der SGS L-10 Baureihe sind in Arbeitsbreiten von 100, 200, 300 und 400 mm und für Granulatlängen von 1 bis 5 mm verfügbar.