Der US-amerikanische Hersteller von Wassersystemlösungen suchte nach einem effizienten Verfahren zur Herstellung von dünnwandigen Auskleidungen für eine neue Reihe von Drucktanks. Mit Hilfe eines Teams von Zulieferern, darunter Inoex, baute das Unternehmen eine moderne Extrusionsanlage.
Amtrol, West Warwick (Rhode Island/USA), erfand vor über 50 Jahren den ersten Druckwassertank zur Wasserversorgung als bessere Lösung für herkömmliche Luft-Wasser-Tanks. Die meiste Zeit dieser Jahre waren die Tanks komplett aus Stahl gefertigt. Doch der Wettbewerbsdruck veranlasste das Unternehmen, nach einer kostengünstigeren Möglichkeit zu suchen, die Produktpalette zu erweitern, ohne dabei Abstriche bei der Qualität zu machen. Die Fragen lauteten: Welches Material wäre für die Anwendung geeignet und wie könnte es hergestellt werden?

Die Behälterwände werden mit spritzgegossenen Kappen drehgeschweißt und einem OD-Stahlband als Verstärkung versehen. (Foto: Inoex)
Ein wichtiger Bestandteil der Tanks ist die Auskleidung. Das ist der innere Behälter, in dem das Wasser unter Druck steht, um eine konstante Durchflussrate in einem Haushalt oder einer anderen Wohnung aufrechtzuerhalten. Amtrol untersuchte eingehend mögliche Materialien und Verfahren, um die Qualitäts- und Kostenziele des Unternehmens zu erreichen. Schließlich entschied man sich mit Hilfe eines Teams von Zulieferern für eine unkonventionelle Lösung. Ken Cerpovicz, der Produktdirektor von Amtrol, erklärt: „Wir haben uns für die Extrusion entschieden, weil sie Flexibilität und Anpassungsfähigkeit für zukünftige Produkte bietet. So können wir uns an die Kundenbedürfnisse anpassen und haben eine große Auswahl an Größen und Abmessungen, die wir verwenden können.“ Die Auskleidungen würden aus Polypropylen hergestellt. Die Körper würden wie Rohre extrudiert, mit einem Deckel versehen und dann mit einer Faserverstärkung umwickelt, um die Festigkeit zu erhöhen.
Die Herausforderung
Laut Jody McKinley, dem Leiter der technischen Abteilung, bestand die größte Herausforderung des Projekts darin, dünnwandige Polypropylenrohre mit großem Durchmesser präzise und ohne Verformung zu extrudieren. Dies war eine seltene technische Anwendung, die bisher nur in wenigen Fällen auf der ganzen Welt durchgeführt wurde.

Die Rohre werden in einem geschlossenen Regelkreislauf extrudiert und an eine Rotationsschweißstation weitergeleitet, um die spritzgegossenen Kappen zu befestigen, anschließend wird die Einheit zur Erhöhung der Festigkeit mit einem Verbundstoff umwickelt. (Abb.: Inoex)
Die Rohre können einen Durchmesser von bis zu 26 Zoll und eine Wanddicke von 0,1 bis 0,15 Zoll haben. Das Endprodukt muss einen Druck von über 150 psi aushalten können. Als ob das nicht schon Herausforderung genug wäre, war dies die erste Erfahrung von Amtrol mit der Extrusion, und ein entscheidender Teil der Projektentwicklung fand in den Tiefen der Covid-Epidemie statt.
Der gesamte Prozess läuft wie folgt ab: Die Behälterwände werden extrudiert und geschnitten. Spritzgegossene Kappen werden drehgeschweißt, um den Behälter zu umschließen. Ein OD-Stahlband wird als Verstärkung für die internen Komponenten angebracht, dann wird die Baugruppe an eine Verbundstoff-Wickelmaschine übergeben, um dieser zusätzliche Festigkeit zu verleihen. All dies geschieht in einem hochautomatisierten Produktionsprozess, bei dem der Extrusionsvorgang von einem einzigen Kontrollsystem gesteuert wird, das die Prozessparameter auf der Grundlage von Inline-Messungen des Rohrs automatisch anpasst.
Die präzise Steuerung des Extruders ist eine zentrale Anforderung und für eine vollständig automatisierte Linie musste jede wichtige Komponente in ein einziges Steuerungssystem eingebunden werden. Um den Kreislauf zu schließen, war es wichtig, Inline-Prozessmessungen zu erhalten, die zur dynamischen Steuerung der Linien- oder Abzugsgeschwindigkeiten verwendet werden. Dadurch kann Amtrol den gesamten Prozess optimieren und sich bei Bedarf automatisch an Prozessabweichungen anpassen.
Die Lösungsfindung
Nach umfangreichen Recherchen entschied sich Amtrol für KraussMaffei, München, als Lieferant des Extruders und als Systemintegrator für das Projekt. KraussMaffei wiederum holte branchenführende europäische Technologiepartner mit ins Boot, darunter Inoex aus Melle, das über umfassende Erfahrung mit gravimetrischen Dosierern, Mess- und Regelsystemen verfügt, die Prozesse auf der Grundlage von Messdaten adaptiv steuern. Sica, Alfonsine (Italien), wurde mit dem Bau der Abzugs- und Abschneidestationen beauftragt.
Nur sehr wenige Verarbeiter haben jemals eine Extrusionsanlage mit einem derartigen Umfang gebaut, so dass es für alle Beteiligten eine Lernerfahrung war. Die großartigen Bemühungen in den Bereichen Technik, Implementierung und Zusammenarbeit trugen letztendlich dazu bei, die Ziele von Amtrol zu erreichen.
Gravimetrische Zuführung zum integrierten Abzug
Auch wenn die Beständigkeit des Extrusionsprozesses wichtig ist, ist das, was an beiden Enden des Extruders passiert, ebenso entscheidend für eine vollautomatische Produktion. Die Vorteile von gravimetrischen Dosierern und Mischern sind allgemein bekannt. Die Steuerung der Materialmenge, die in den Extruder gelangt, erfolgt über das Gewicht und nicht über das Volumen, was insbesondere bei Schwankungen in der Schüttdichte des Materials genauer ist. Und die Zuverlässigkeit der Materialzufuhr war bei dieser Anwendung sicherlich wichtig. Besonders entscheidend ist jedoch die Integrationsfähigkeit der Inoex Saveomat. Sie lässt sich in die KraussMaffei-Extrudersteuerung integrieren und bietet die Möglichkeit, Regelkreise auf Basis des Metergewichts einzurichten, in denen die Abzugsgeschwindigkeit dynamisch angepasst werden kann, um die richtige Wandstärke zu erzeugen, oder auf Basis des Massedurchsatzes, der durch Erhöhen oder Verringern der Schneckendrehzahl gesteuert wird.

Das gravimetrische Dosiersystem sorgt für eine präzise Dosierung und seine Steuerung spielt eine wesentliche Rolle bei der Systemintegration. (Foto: Inoex)
Im weiteren Verlauf sind die Sica-Abzüge mit Quetschschutzsensoren ausgestattet, die für die Arbeit mit dünnwandigen Rohren ausgelegt sind. Zehn unabhängig voneinander angetriebene Abzugsbahnen, die um den Rohraußendurchmesser herum angeordnet sind, bieten die für eine maximale Abzugskraft erforderliche große Kontaktfläche. Zwar ist eine gewisse Verformung des Strangpressprofils erforderlich, um eine ausreichende Zugkraft zu erzielen, doch wird dadurch gerade genug Druck erzeugt, um die Arbeit zu erledigen. Ein sauberer Schnitt an der Kante der Zylinder erwies sich ebenfalls als Herausforderung, aber die große Auswahl an verfügbaren Schneidwerkzeugen von Sica lieferte die gewünschte Schnittqualität.
Die Messung ist der Schlüssel
Der Schlüssel zum Zusammenspiel des gesamten Systems ist das Wandmesssystem AFM6300 von Inoex. Die Messstation basiert auf Ultraschalltechnologie und ist in der Lage, die Wandstärke, den Durchmesser und die Rundheit von Rohren präzise zu messen. Üblicherweise werden Systeme wie dieses nicht nur zur Qualitätskontrolle eingesetzt, sondern auch, um den Extrusionsprozess näher an die erforderliche Mindestwandstärke heranzuführen, was zu erheblichen Materialeinsparungen führen kann. Bei sehr dünnwandigen Rohren, wie sie Amtrol herstellt, liegt der Schwerpunkt eher darauf, sicherzustellen, dass das Produkt die sehr anspruchsvollen oberen und unteren Toleranzen für die Wandstärke einhält. Auch die Rundheit ist wichtig, da die Rohre in einem vollautomatischen Prozess verschlossen werden.
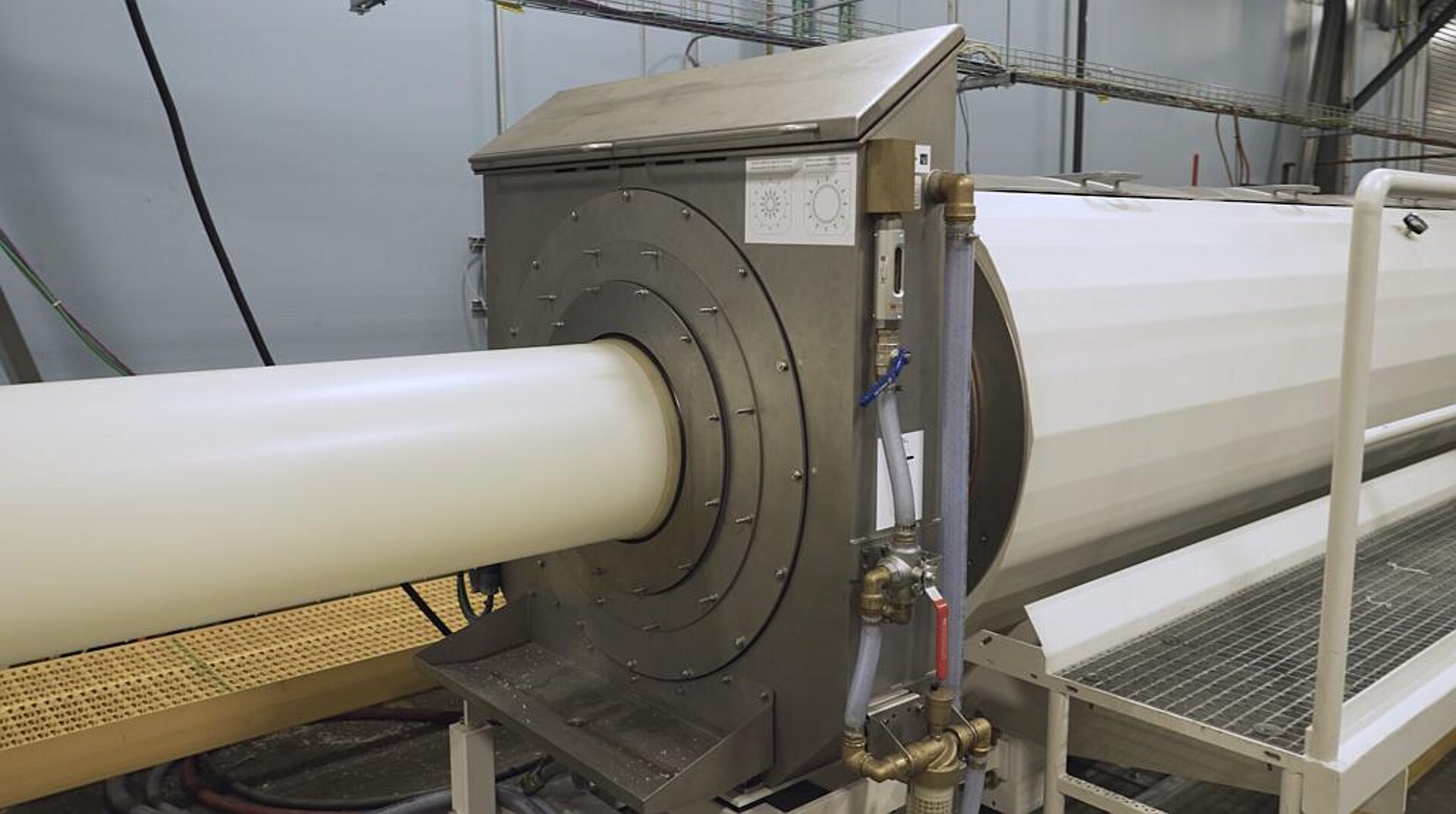
Das Inoex-Ultraschallmesssystem, das sich direkt außerhalb des Vakuumtanks befindet, liefert präzise Dimensionsdaten, die in den geschlossenen Regelkreis eingespeist werden. (Foto: Inoex)
Im Betrieb arbeitet ein Ultraschallsensor nach dem Prinzip der Lichtlaufzeit, um sehr präzise physikalische Messungen zu berechnen. Während das Rohr durch einen dünnen Wassermantel läuft, senden die Sensoreinheiten eine Ultraschallwelle aus, die als Echo zurückkommt, wenn sie auf ein Objekt trifft. Bei der Rohrextrusion entsteht das erste Echo, wenn ein Impuls auf den Außendurchmesser des Rohrs trifft, das zweite, wenn er auf die Innenwand (oder genauer gesagt, auf das dahinter liegende Medium) trifft. Durch die Messung der Zeit, die zwischen der Übertragung und den Echos verstreicht, können sehr schnelle und präzise Dimensionsmessungen für Wandstärken von nur 0,01 mm berechnet werden. Die robuste Ultraschallmesstechnologie von Aurex liefert vollständige Daten, die zur Prozessoptimierung oder Qualitätsdokumentation genutzt werden können.
Die wichtigste Aufgabe von Amtrol ist jedoch die Bereitstellung von Messdaten in Echtzeit, die den Schlüssel zur vollständigen Prozesssteuerung darstellen. Kontrollsysteme mit geschlossenem Regelkreis wie dieses können auf verschiedene Weise konfiguriert werden. Bei Amtrol werden die Messdaten an das gravimetrische System gesendet, das die einzelnen Komponenten der Anlage misst und steuert. Das C6-Steuerungssystem von KraussMaffei ermittelt anhand der Messergebnisse, ob die Anlagengeschwindigkeit angepasst werden muss, um ein konstantes Metergewicht des Produkts zu gewährleisten.

Der Bau der Extrusionsanlage mit einem derartigen Umfang war für alle Beteiligten eine Lernerfahrung. (Foto: Inoex)
Das Aurex-System misst die Produktabmessungen und bestimmt anhand der gemessenen Mindestwandstärke, ob der Sollwert für das Metergewicht gesenkt oder erhöht werden muss. Nähert sich eine dünne Stelle der Mindesttoleranz, erhöht der Dünnstellenregler den Sollwert des Metergewichtsreglers in der Extrudersteuerung.
Alles unter Kontrolle
Laut dem technischen Leiter von Amtrol, Jody McKinley, bestand eine große Herausforderung darin, die Formel für die Synchronisierung aller Produktionskomponenten – Zuführung, Extruder, Vakuumtank und Abzug – zu finden, um das benötigte Produkt zu liefern. Entscheidend für den Erfolg war jedoch, den Prozess tagein, tagaus unter Kontrolle zu halten. Er sagt: „Das Produkt muss gleichbleibend und einheitlich sein. Dank der Zusammenarbeit mit unseren Maschinenherstellern konnten wir den Prozess mit Datenanalysen und SPC-Kontrollen versehen, um die Prozessvariablen zu minimieren. Dadurch sind wir in der Lage, ein gleichbleibendes Produkt über einen längeren Zeitraum zu produzieren“, sagt er.

Zusammenarbeit im Team: Adam Grier von Inoex, Artie Riegger von KraussMaffei und Alex Spires, Projektleiter von Amtrol. (Foto: Inoex)
Amtrol ist eines der wenigen Unternehmen weltweit, das einen leichten, hochleistungsfähigen Druckbehälter mit einer derart dünnwandigen Konstruktion herstellen kann. Als Ergebnis genießen die Kunden von Amtrol die Vorteile eines langlebigen, wettbewerbsfähigen Produkts mit einzigartigem Anwendernutzen. Die kreative Anwendung des Extrusions-Know-hows eines Teams von Prozess- und Entwicklungsexperten hat sie dazu gebracht.