Die Verfahren des Unternehmens ermöglichen hochwertige Produkte aus recyceltem Kunststoff. Auf der Kuteno zeigt Deckerform mit PolyFoamFiber und PolyFoamX, wie hochwertige Bauteile mit technischer Raffinesse und ressourcenschonendem Einsatz entstehen.
Das Aichacher Familienunternehmen präsentiert live am Messestand die vollelektrischen Spritzgießmaschinen des japanischen Herstellers Toyo, die Deckerform im deutschsprachigen Raum exklusiv vertritt. Ebenso zeigt das Unternehmen seine neusten Entwicklungen rund um das material- und gewichtssparende Produktionsverfahren Spritzschäumen, auch bekannt als Thermoplast-Schaumspritzgießen (TSG). Diese zeigen, wie sich hier gerade auch beim Einsatz von Recyclingmaterialien Produkte mit gut definierbaren mechanischen, haptischen und optischen Effekten herstellen lassen.
Dass Werkstücke mit Spritzschaumguss aus Recyclingmaterialien edle Oberflächen haben können, hat Deckerform bereits mehrfach demonstriert. Dass sich auf diese Weise darüber hinaus auch gezielt Werkstücke mit genau abgestimmten mechanischen Eigenschaften erstellen lassen, zeigt das Unternehmen unter anderem mit dem Verfahren PolyFoamFiber und dem Prototypen einer neuen Generation von Stühlen.
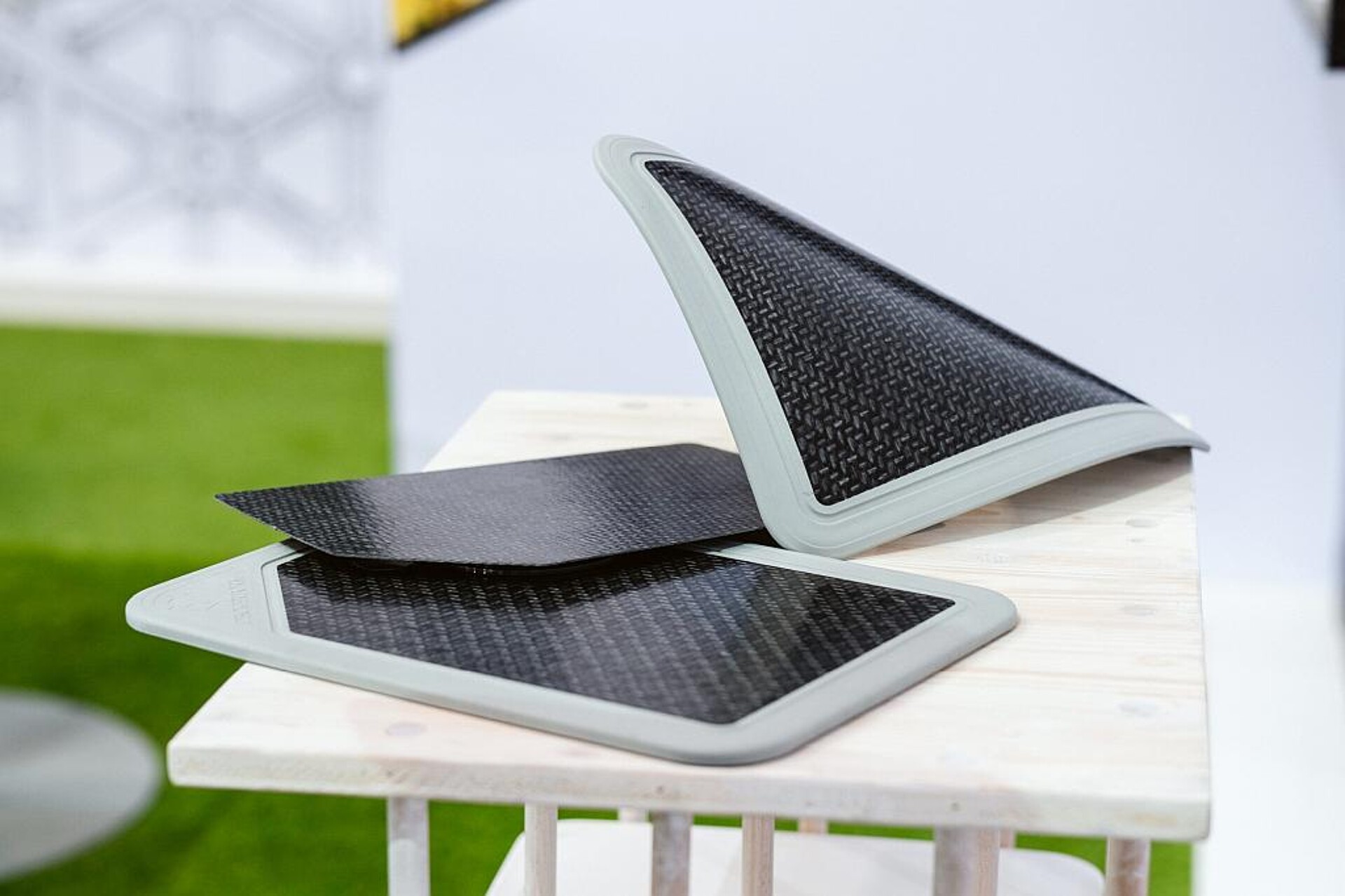
Mit PolyFoamFiber werden Organosheets mit spritzgeschäumtem Füllmaterial für steife, leichte und nachhaltige Verbundbauteile kombiniert. (Foto: Deckerform)
Fasern im Fokus
Bei PolyFoamFiber werden Organosheets in ein Tauchkantenwerkzeug eingelegt und mit einem Füllmaterial hinterspritzt. „Das kann theoretisch auch Recyclingmaterial sein“, erklärt Deckerform-Geschäftsführerin Anna Tschacha. „Die wesentlichen mechanischen Eigenschaften des Bauteils wie etwa die Zugstabilität lassen sich dabei über die Organosheets definieren – das können Kohle- oder Glasfasern ebenso sein wie Pflanzenfasern, etwa Hanf oder Flachs. Inmitten befindet sich dann chemisch geschäumtes Recyclingmaterial, das mit den außenliegenden Organosheets eine belastbare Verbindung eingeht. Der Verbund sorgt in materialsparender, effizienter und sehr steifer Leichtbauweise für die Stabilität des Kunststoffverbundteils.“
„Wir können jedem nur nahelegen, Leichtbau durch Schäumen auszuprobieren. Der Vorteil beim chemischen Schäumen ist, dass es im Vergleich zu physikalischen Verfahren kaum Investitionskosten mit sich zieht. Für uns ein hervorragender Weg, um ressourcenschonender mit Kunststoff umzugehen – und das sogar mit mehr Stabilität, Isolationswirkung und weniger Gewicht“, so Tschacha.
Beim Prototyp für einen Stuhl wollen die Aichacher die Komponente neu definieren, die für die Bewegung der Sitzfläche gegenüber dem Untergestell des Stuhls verantwortlich ist. Im Normalfall übernimmt eine komplexe Mechanik diese Aufgabe. In der Ideenschmiede bei Deckerform hat ein Team um Kunststoffingenieur Peter Ottilinger diese Herausforderung neu gedacht und mit PolyFoamFiber eine Lösung entwickelt. Diese kommt ohne eine komplexe Kinematik aus und ermöglicht die Relativbewegung zwischen Sitzfläche und Untergestell allein aus der Elastizität eines spritzgeschäumten Bauteils heraus.
Dynamik durch Werkstoffdesign
„Dabei lassen sich die mechanischen Eigenschaften, etwa der Grad der Elastizität, sehr gut über die Geometrie des Bauteils definieren, etwa, indem man bestimmte Partien beispielsweise breiter oder schlanker ausführt“, erläutert Tschacha. „Das Teil selbst kann als One-Shot-Produkt gefertigt werden – inklusive des Einlegens der Organosheets ins Werkzeug ist das in einem Arbeitsschritt auf der Maschine erledigt. So lassen sich auch größere Stückzahlen mit überschaubaren Zykluszeiten sehr rationell fertigen.“ Dass dieses Produkt ein ganzes Möbelleben hält – davon sind die Kunststoffspezialisten überzeugt.
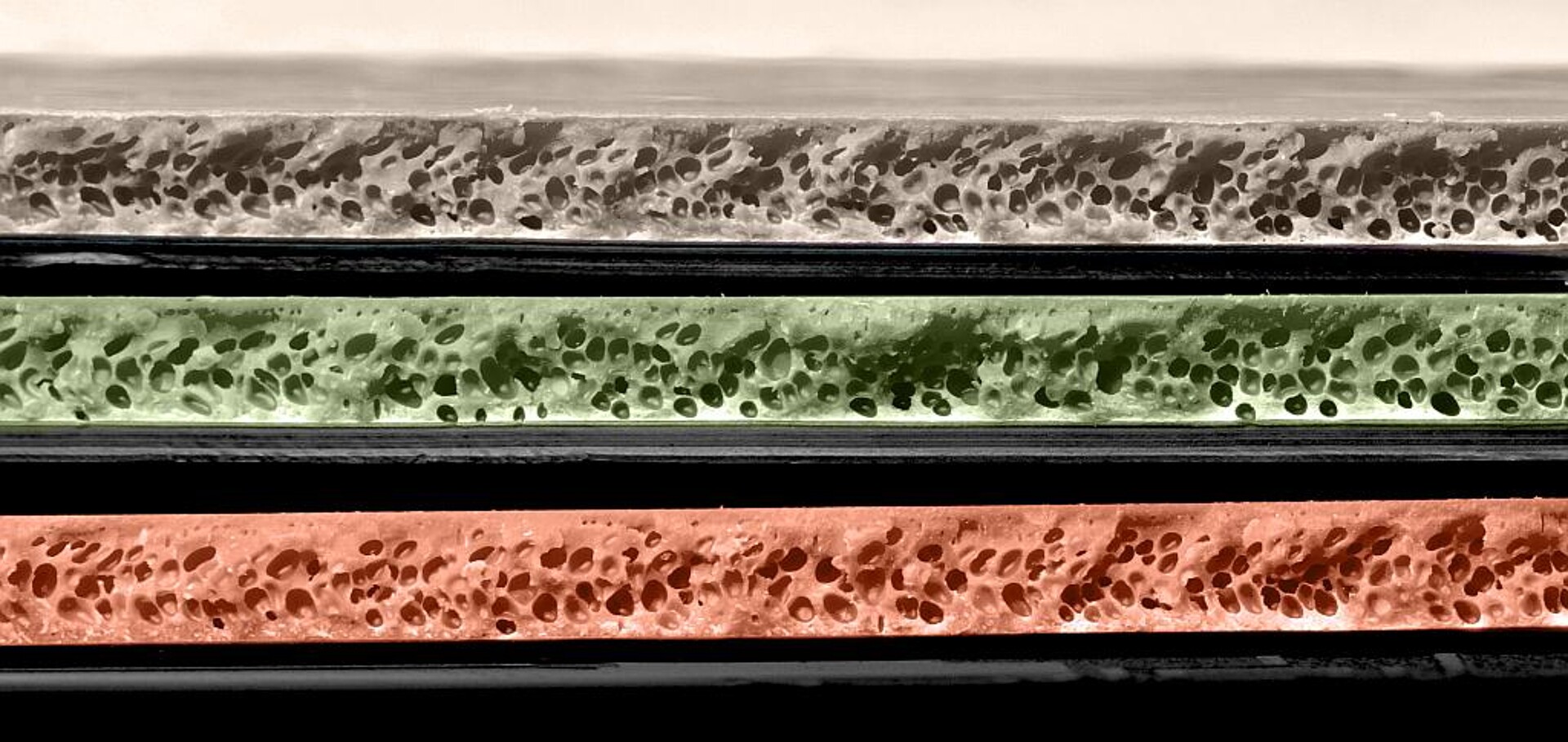
Mikrozelluläre Schaumstruktur vom Kunststoff im Inneren von Teilen, die mit den Verfahren PolyFoamX hergestellt wurden. (Foto: Deckerform)
Mit PolyFoamX hat das Unternehmen eine Technologie speziell für kleinere Stückzahlen bei flächigen Kunststoffteilen entwickelt. Dabei wird zunächst ein sehr dünnwandiges Vollmaterial-Teil gespritzt, das dann für den Teilekörper selbst per Spritzschäumen hinterspritzt wird. Bereits auf früheren Messen zeigten die Aichacher damit unter anderem anhand eines Caféhaustabletts als Beispielteil die grundsätzlichen Möglichkeiten des Verfahrens auf.
Weniger Wand, mehr Wirkung
Mit dem live auf der Kuteno produzierten Kunststoff-Label zeigt Deckerform, dass es auch dünner geht. Verbunden mit dem IMD-Verfahren und hochfiligranen Laserstrukturen, entstehen hier 3D-Label, welche beispielsweise hochwertige Spirituosen- oder Kosmetikflaschen zieren oder auch Logos und andere Designelemente detailliert und plastisch darstellen. Auf dem Messestand präsentiert das Unternehmen unter dem Motto „Beyond Luxury. Beyond Expectations.“ zusammen mit Partnern eine Beispielanwendung, die die Möglichkeiten des Verfahrens zeigt. Die Aichacher wollen mit diesem Projekt insbesondere Designer und Produktentwickler der Branche ansprechen und die gestalterischen Möglichkeiten mit Kunststoff demonstrieren.
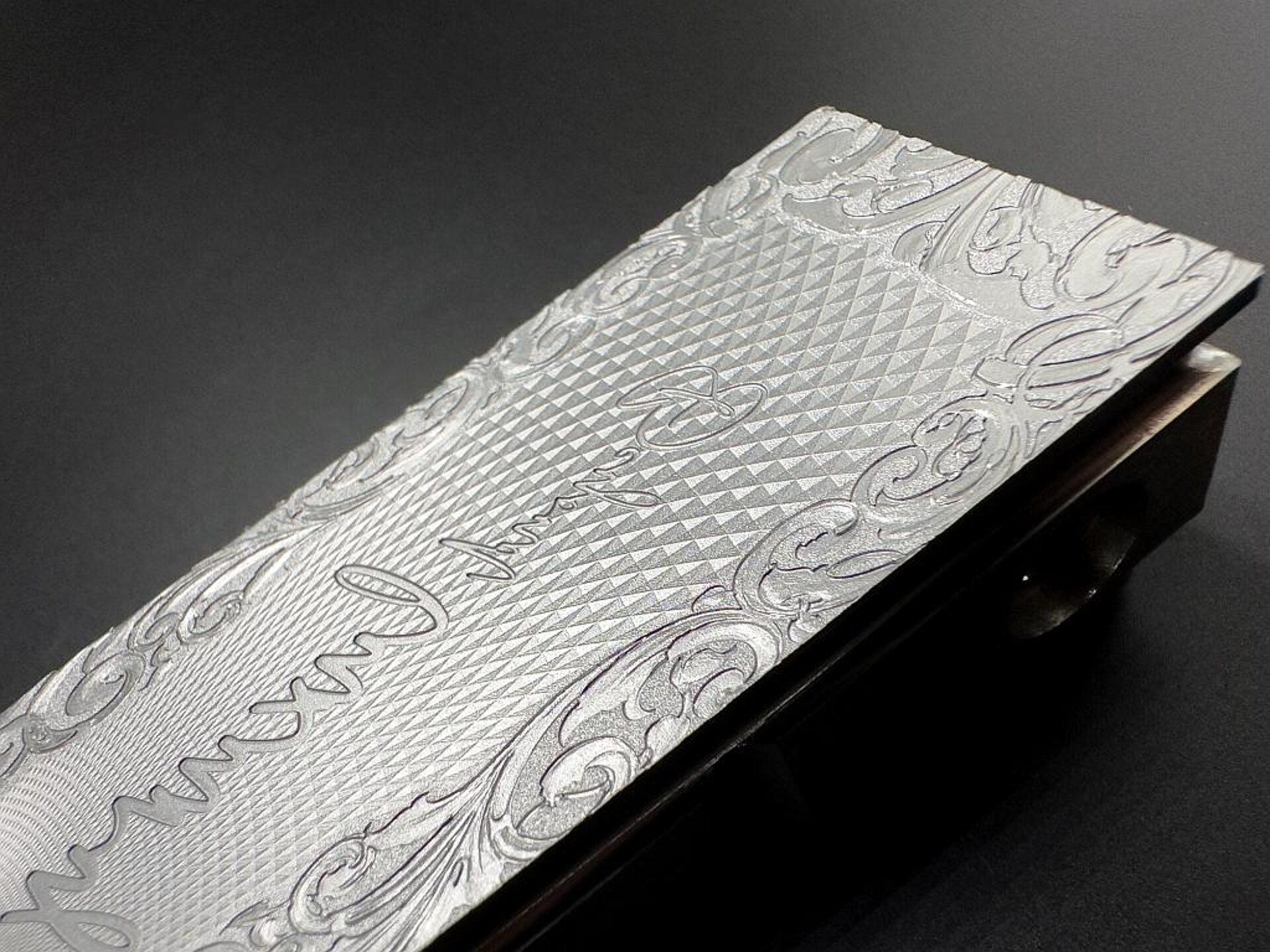
Auf der Kuteno produziert Deckerform live 3D-Kunststoff-Labels mit edler Oberflächenstruktur – gefertigt im IMD-Verfahren mit Lasertechnologie. (Foto: Deckerform)
Wenn Spezialisten Synergien bilden
Für das Heißkanalwerkzeug, das bei Deckerform gefertigt wurde, lieferte der österreichische Normalien- und Heißkanalspezialist Meusburger aus Wolfurt die Komponenten. Die edle Optik lieferten die Oberflächenspezialisten im Reichle Technologiezentrum in Bissingen/Teck mittels Lasereinbringung einer filigranen Oberflächenstruktur. Ins Werkzeug wird per Folie des Dünnschichttechnologiespezialisten Leonhard Kurz Stiftung & Co. KG aus Fürth eine dünne Lackschicht in die Kavität eingebracht, die dann per Spritzprägen auf einer vollelektrischen Toyo-Maschine hinterspritzt wird.
Das Ergebnis ist eine hochwertige Anmutung, die die filigrane Struktur exakt wiedergibt. „Als Material, das wir hinterspritzen, verwenden wir auf der Messe zwar PP-Neuware. Theoretisch sind trotz der hohen Anforderungen an solche Teile aber auch Rezyklate geeignet – sogar Post-Consumer-Material etwa aus der gelben Tonne“, betont Tschacha. „Wir ermöglichen es, Recyclingverbünde in einem weiten Spektrum an Produkten einzusetzen – überall, in allen Branchen und auch bei höchsten Ansprüchen etwa an die Oberfläche.“
Kompakt, energieeffizient und produktionsstark
Auf der Kuteno zeigt Deckerform live am Messestand die Herstellung eines hochwertig strukturierten Kunststofflabels – 157 x 37 mm groß, mit einer Wandstärke von rund 0,5 mm und einem Gewicht von 30 g. Produziert wird auf einer vollelektrischen Spritzgießmaschine Toyo Si-50-6s D75E.
Mit ihrem Schneckendurchmesser von 28 mm ermöglicht die ausgestellte Maschine ein Einspritzvolumen von bis zu 69 cm³. Die sehr kompakte 500-kN-Maschine gibt es alternativ auch mit einem kleineren Schneckendurchmesser von 16 mm und einem Einspritzvolumen von 13 cm³. Die Einspritzgeschwindigkeit von bis zu 300 mm/s und ein maximaler Einspritzdruck von 1.830 bar bieten ausreichend Leistungsreserve für komplexe Geometrien und anspruchsvolle Werkstoffe. Trotz ihrer kompakten Bauweise von rund 2,8 t liefert die Si-50-6s D75E einen großzügigen Holmabstand von 360 x 360 mm „Damit kommt man in dieser Werkzeugklasse in der Regel sehr gut zurecht“, erklärt Tschacha. „Auf der Maschine sind Werkzeuge bis zu einer Plattengröße von 500 x 500 mm möglich.“