Seit 20 Jahren ist der In-Mould-Coating-Pionier in der Konstruktion und Herstellung von PU-Werkzeugen aktiv. Eine der neuesten Entwicklungen ist eine effiziente Technologie für dünnste PU-Schichten.
Die Polyurethan-Erfahrung der Siegfried Hofmann GmbH, Lichtenfels, reicht bis ins Jahr 2004 zurück. Damals entwickelte das Unternehmen sein erstes In-Mould-Painting-Versuchswerkzeug mit PU: Die damals revolutionäre Technologie erlaubte die Herstellung von Spritzgussteilen mit hochglänzenden Oberflächen in einem einstufigen Prozess.
Das erste, große PU-Coating Werkzeug mit widerstandsfähiger PU-Beschichtung entstand im Rahmen eines Messeprojekts: Mit zwei unterschiedlichen Polyurethanen, zwei Mischköpfen, ABS sowie PMMA wurde das 4K-Werkzeug auf der K-Messe 2010 vorgestellt. Die Lösung für kratzresistente, hochglänzende Oberflächen substituiert das klassische Lackierverfahren und überzeugt vor allem die Automotive-Branche, da das Ausschussrisiko vom regulären Lackierprozess deutlich unterboten wird.
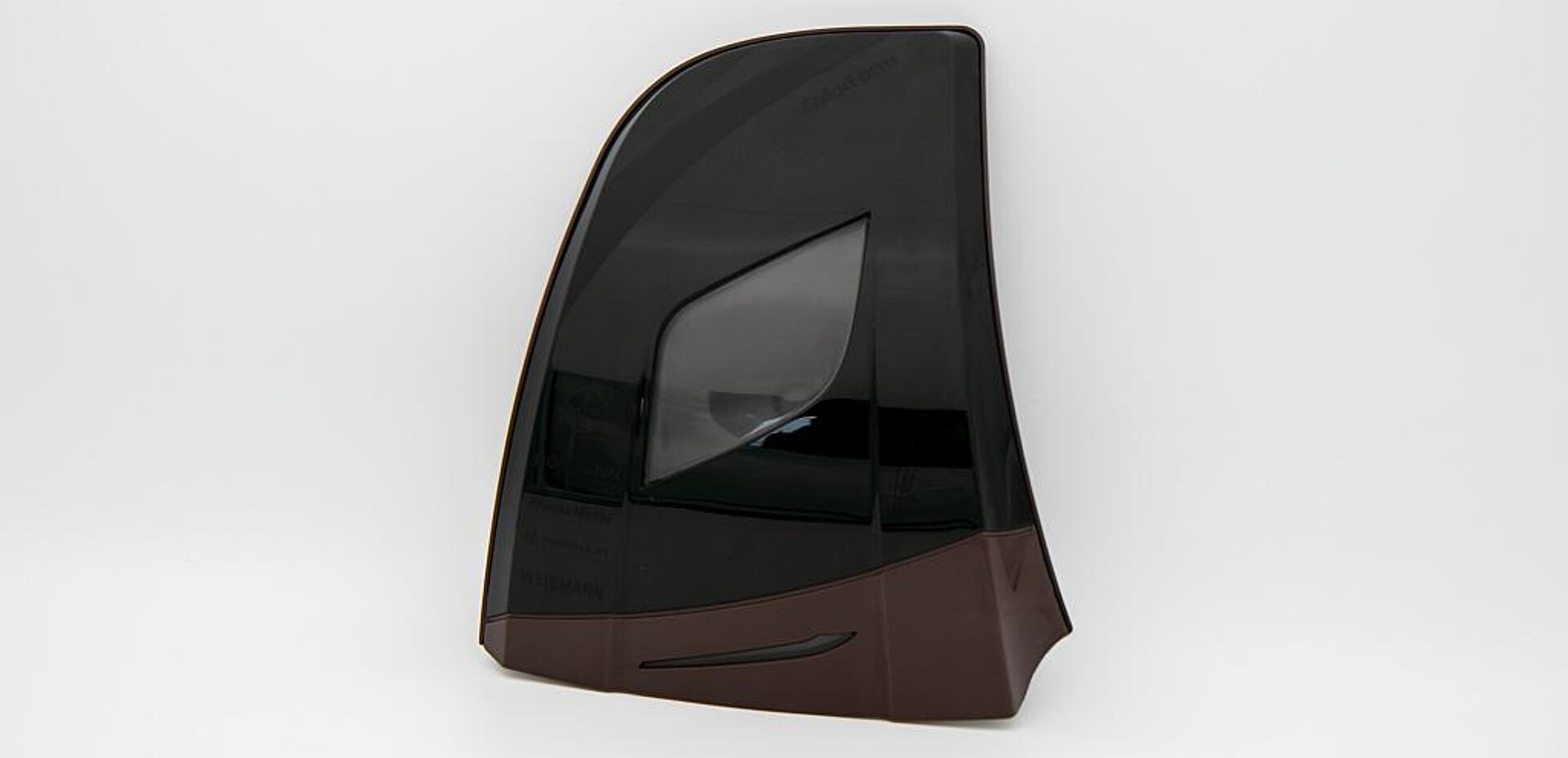
Erstes PU-Coating-Produkt mit zwei unterschiedlichen Polyurethanen aus dem Jahr 2010. (Foto: Hofmann)
Ab dem Jahr 2011 folgten zahlreiche Werkzeuge für große Instrumententafeln, Blenden, Armlehnen oder Türpaneele. Das Serienproduktions-Debüt mit einem PU-Werkzeug von Hofmann startete 2016 zur Fertigung von kratzresistenten, hochglänzenden A-Säulen bei einer Zykluszeit von 60 s für einen französischen Automobilhersteller.
Dank seiner langen Historie mit über 80 umgesetzten PU-Werkzeugen bietet Hofmann eine umfassende Expertise auf diesem Feld. Traditionell profitieren PU-Werkzeuge bei Hofmann unter anderem von einem exklusiven Abdichtdesign, welches das Überlaufen des sehr flüssigen PUs während des Spritzvorgangs verhindert. Somit beugt diese Konstruktionslösung unschöner Gratbildung vor und sorgt für besonders hochwertige Oberflächen.
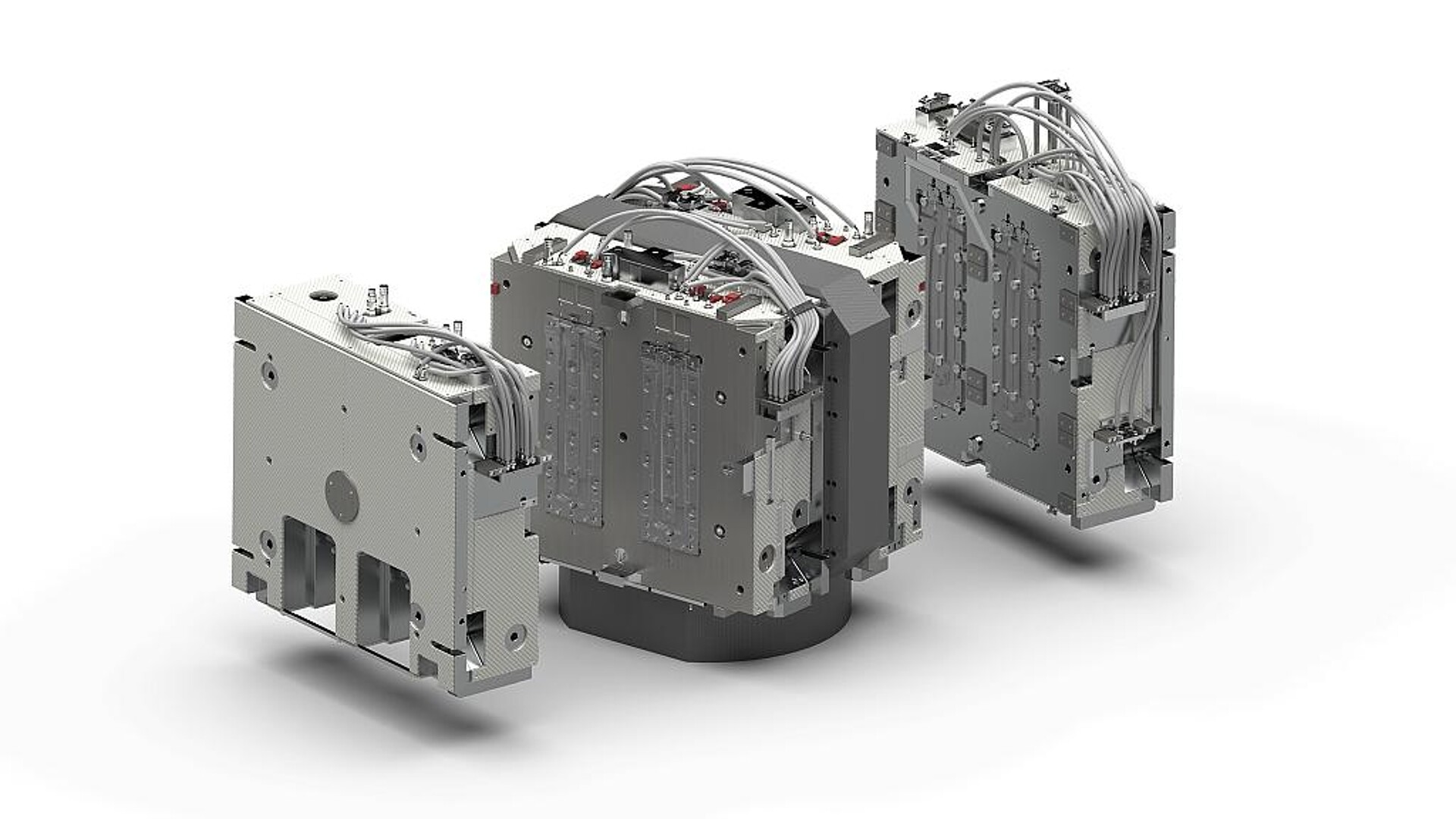
Dieses 2K-Wendeplattenwerkzeug kombiniert PU und Spritzprägen für die Serienproduktion. (Foto: Hofmann)
Insbesondere neue Technologiekombinationen, wie von PU, Spritzprägen und smarten Folien in nur einem Werkzeug, bieten Vorteile hinsichtlich Zykluszeit, Produktdesign und Prozesseffizienz. Diese Synergieeffekte sind aktuell in Form von Ambient Lighting Interieur Blenden, Front End, Diffusoren oder Exterieur Blenden bei vielen deutschen Premium-Automobilen sichtbar.
Aktuell feilt das Familienunternehmen an einer bereits patentierten Technologie für besonders dünne PU-Schichten. Ziele sind neben der Materialersparnis auch positive, ökologische Effekte hinsichtlich des Gewichts, CO2-Fußabdruck und Energieverbrauch, da klassische PU-Dicken von circa 0,5 bis 0,8 mm deutlich unterboten werden sollen.