Der Polymerspezialist und der 3D-Druckerhersteller haben eine Technologie zum Drucken von kompletten Booten entwickelt. Zum Einsatz kommt das speziell dafür designte High-Performance-Polyolefin CeadHDPro.
Vor zwei Jahren begann die Zusammenarbeit von Uwe Stenglin, CEO der Rotfeld-Consulting GmbH & Co. KG und Hauptgesellschafter der Dipromat GmbH, Adelshofen, mit der Cead B.V., Delft (Niederlande), die Granulat-Drucker für das LFAM (Large Formate Additive Manufacturing) herstellt.
Für die Herstellung von Booten aus Kunststoff stehen sich zwei grundsätzliche Werkstoff-Familien gegenüber: Zum einen Polyesterboote mit Laminier-Technik und Glasfaser- oder Carbon-Faser Verstärkung. Diese Materialen zeigen hohe mechanische Werte, aber auch hohe Dichte, geringe Bruchdehnung, sehr hohen handwerklichen Arbeitsaufwand und keine sinnvolle Recyclingfähigkeit. Dagegen steht Polyethylen als gut verarbeitbarer, zäher Thermoplast, welcher in der Bootsindustrie einen festen Platz hat. Die Dichte ist gering und die Recyclingfähigkeit sehr gut.
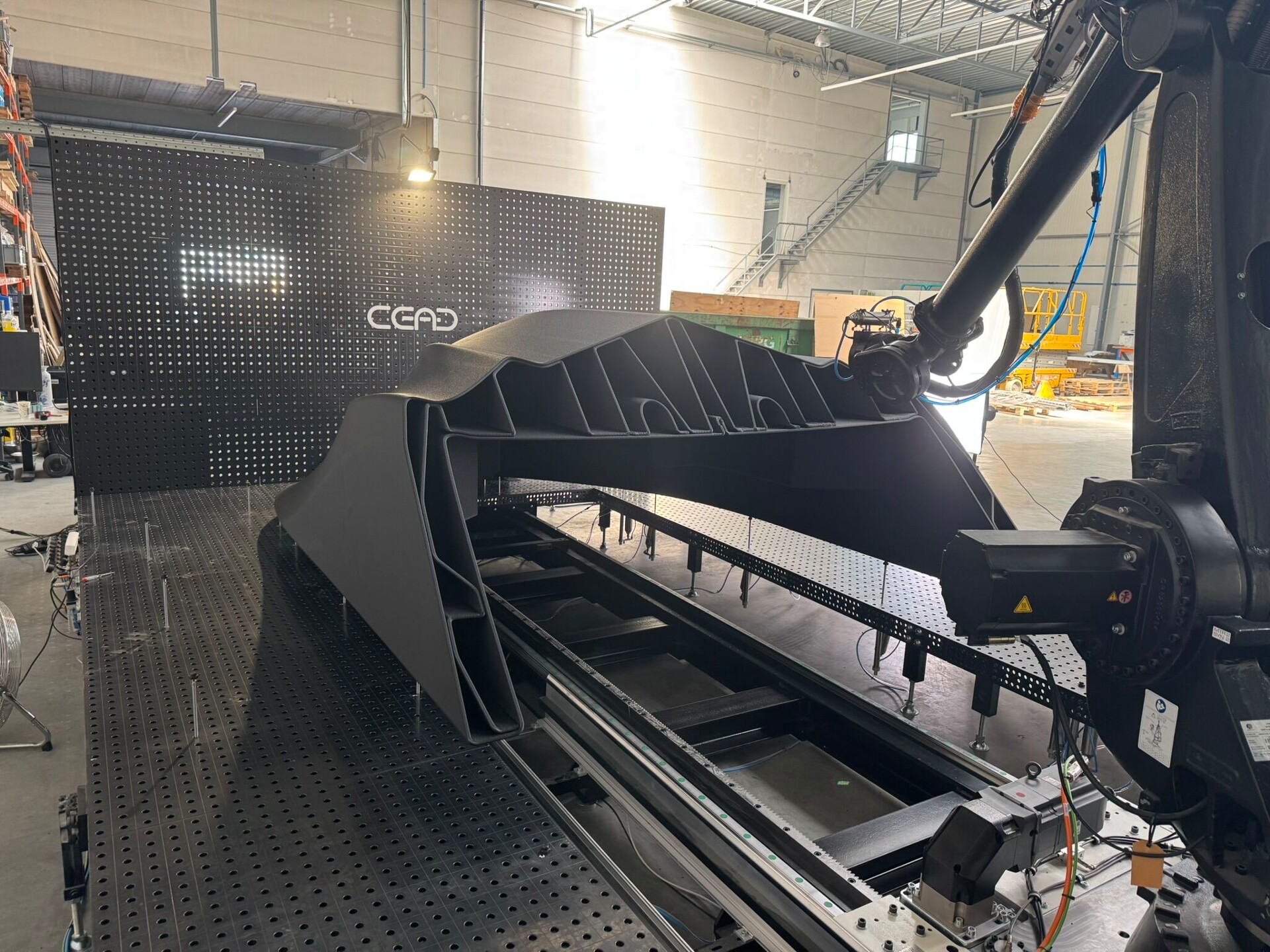
Das für Heavy-Duty Marine Applications maßgeschneiderte Polymer wurde zum Drucken von Booten entwickelt. (Foto: Cead)
Nachteil ist, vor allem für große Boote, die geringe Steifigkeit und der hohe Arbeitsaufwand bei der Verarbeitung von HDPE-Plattenware mit viel Verschnitt. Zudem müssen die hohe Wärmedehnung und die Spannungsrissbildung bei HDPE berücksichtigt werden. Die gegen Rissbildung unempfindlicheren PE-Typen wie MDPE, LDPE, LLDPE oder VLDPE sind durch die vorhandenen Verzweigungen gut auch in der Kerbschlagzähigkeit und immer besser als HDPE mit geringen Verzweigungen. Thermische Werte und Steifigkeit sowie Festigkeit gehen allerdings deutlich zurück. Durch die sehr hohen Formschwindungen von 1,5 bis 2,5 % sind PE-Polymere kaum druckbar. Je größer die Boote werden, umso schwieriger wird die Verarbeitung.
So entstand die Aufgabenstellung einen umweltfreundlichen Thermoplast mit folgenden Vorgaben zu entwickeln:
- Verträglichkeit mit HDPE und die Möglichkeit thermoplastischer Verschweißung mit Heißluftgeräten muss möglich sein
- Eigenschaften weit über HDPE hinaus
- leicht zu recyceln mit PE/PP/PO
- hoher E-Modul, deutlich steifer als HDPE
- hohe Schlag- und Kerbschlagzähigkeit, HDPE ist zwar sehr schlagzäh, aber sehr schlecht kerbschlagzäh, was bei robusten Anwendungen ein Problem sein kann
- höhere Zugfestigkeit als HDPE
- geringe Schwindung und Dimensions-Stabilität für LFAM
- geringe Dichte
- UV-stabil
- geringe Wasseraufnahme
- Hydrolyse-Festigkeit
- Hitzebeständigkeit > 80 °C
Das Ergebnis ist das spezialglasfaserverstäktes Polyolefin CeadHDPro – Engineered for Heavy-Duty Marine Applications – das alle geforderten Eigenschaften mitbringt. Schweißdrähte aus gleichen Polymeren, ebenfalls mit Glasfaserverstärkung, runden die Technologie ab.
CeadHDPro behält seine Eigenschaften im Bereich von -20 bis +70 °C. Die Kerbschlagzähigkeit bei -20 °C ist noch 5 x höher als die von HDPE bei Raumtemperatur. Die Kerbschlagzähigkeit zwischen Raumtemperatur und 70 °C ändert sich kaum messbar.
Da Maschineneinstellung und Eigenschaften der gedruckten LFAM-Teile ebenso wichtig sind wie das Polymer, werden die Polymere im Gesamtpaket, inkl. Prozessparameter, von Cead vertrieben.
Mit ähnlichen Werkstoffen werden Teile in der Automobilindustrie und Gebäude-Konstruktion hergestellt.
Alle erfolgreichen Polymere für Großraumdrucker haben eine Karriere im FFF/FDM-Druck für kleinere und mittlere Teile, wobei heute auch Filament-Drucker für große Formate verfügbar sind. Die Präzision der Filament-Drucker stehen im Wettbewerb zu günstigen Polymeren bei Granulat-Druckern. Wegen der hohen Anforderungen an möglichst geringe Schwindung sind auch im Granulat-Drucker meist Spezialpolymere im Einsatz. Zum Verschweißen der Großteile sind werkstoffgleiche Filamente oder Schweißdrähte von Vorteil damit die Schweißnaht keine Schwachstelle erzeugt.